Article
Speed business optimization by focusing on these top 10 areas of unintentional waste
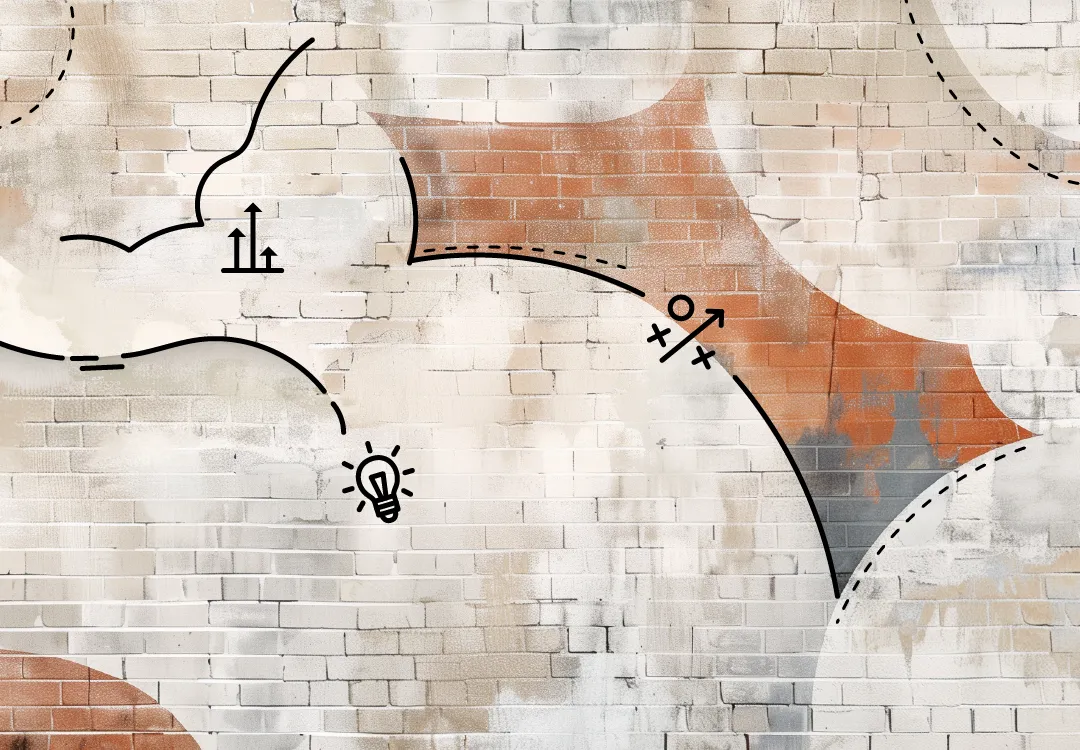
Table of contents
Related services and insights
Organizational performanceAre employee ideas the hidden key to operational efficiency?
Business optimization is a strategic imperative and essential for adapting to today’s environment. The ability to improve quality, productivity, and speed to market while optimizing time, talent, and cost is the difference between just getting by and getting ahead. The good news? Unlocking paths to speed business optimization doesn’t have to be difficult.
Optimizing performance matters now more than ever
A confluence of external factors has created an environment without precedent or playbooks. Razor-thin margins and rising costs are cutting into profitability and growth. Innovation cycles are lightning fast. Keeping pace with technology is a moving target. And the volatile geopolitical climate is impacting business confidence and investment. Organizations need every advantage they can get. Yet many have inefficient processes, lagging productivity, high operational costs, quality issues, and more. They haven’t optimized their business on the inside to respond well to what’s happening on the outside.
Speed business optimization by inventorying your business’s waste hotspots
Business optimization is a holistic process involving changes to systems, structures, workflows, data, technology, and personnel in line with business objectives. While it’s a significant undertaking, it doesn’t have to involve massive ERP overhauls or years’ long initiatives. Organizations can optimize operations in practical ways that deliver results at market speed.
Focusing first on common waste hot spots can jumpstart momentum and deliver quick wins. Start with an efficiency inventory. Ask these key questions about your organization’s performance in the top ten areas of unintended waste.
1
Time waste: Idle time, overprocessing time, and delays
- Are delays or bottlenecks slowing down our work processes?
- Are we spending more time than necessary on tasks, like excessive meetings or redundant approvals?
- Is inefficient scheduling, long lead times or unplanned downtime causing our teams to fall behind?
2
Process inefficiencies: Manual work, duplicative efforts, and complexity
- What manual tasks could we automate to save time?
- Are multiple employees or teams duplicating efforts without coordination?
- Are workflows too complicated, leading to mistakes and slowdowns?
3
Information waste: Poor communication, data silos, and excessive documentation
- Are we miscommunicating or giving unclear instructions that are creating confusion or delays?
- Is a lack of data sharing amongst our teams, departments, and divisions causing duplication of work?
- Are we generating reports and documentation that aren’t needed, have been superseded or don’t add value to our business?
4
Resourcing inefficiencies: Material and energy waste
- Do we have excess materials or poor inventory management leading to waste?
- Are we using business resources inefficiently in our operations, facilities, and production lines?
- Are we leveraging sustainable practices and technologies to minimize adverse impacts in our resource and utility management?
5
Overproduction: Excess output and premature development
- Are we producing more goods or services than necessary or too soon?
- Are we investing time in features or functions that don’t meet immediate needs?
- Are we over-servicing demands in ways that exceed industry standards, creating avoidable waste that could be addressed through targeted corrective actions upstream to enhance operational efficiency?
6
Defects and errors: Rework and nonconformance
- Are we investing business resources to fix mistakes in upstream processes or services?
- Are we failing to meet quality standards in our processes, services, or deliverables?
- Are gaps in our quality standards negatively affecting our downstream teams?
7
Misuse of talent: Underutilization and misalignment
- Are our employees working below their skill level or not being effectively utilized?
- Are we assigning tasks that don’t align with employees’ expertise or our business priorities?
8
Transportation and motion waste: Excessive movement
- Are we moving materials or data unnecessarily between locations?
- Is inefficient movement, like searching for items or navigating cluttered physical or virtual workspaces, affecting our productivity?
- Are our employees navigating bureaucratic obstacles or distractions that hinder their productivity in the workplace?
9
Financial waste: Overstaffing, understaffing, and inefficient procurement
- Are we aligning our staffing levels with actual, activity-based workload demands rather than relying on proportional estimates, to avoid increased costs or unmet service needs?
- Are we overpaying for supplies due to poor contract management or a lack of competitive sourcing?
- Are we regularly reviewing our staffing strategies and procurement processes to identify obsolete roles in order to eliminate outdated practices that lead to unnecessary expenditures?
10
Missed opportunities for government efficiency: Unseen innovations and uncaptured value
- Are we failing to adopt new technologies or methods that could enhance our efficiency?
- Is a lack of efficiency preventing us from maximizing our impact?
- Are we missing opportunities to learn from best practices in other organizations or industries that could accelerate our productivity and effectiveness?
By identifying common activities and processes that don’t deliver value yet consume time, money, and resources, organizations can establish a foundation for speeding business optimization success. Significant work lies ahead. But reducing waste now can substantially lower operational costs, speed time to market, and enhance customer and employee satisfaction—which are all essential to competitiveness.
Let’s get started
Join 100+ clients from public, private and nonprofit sectors who leverage Eagle Hill’s industry expertise to guide their business.
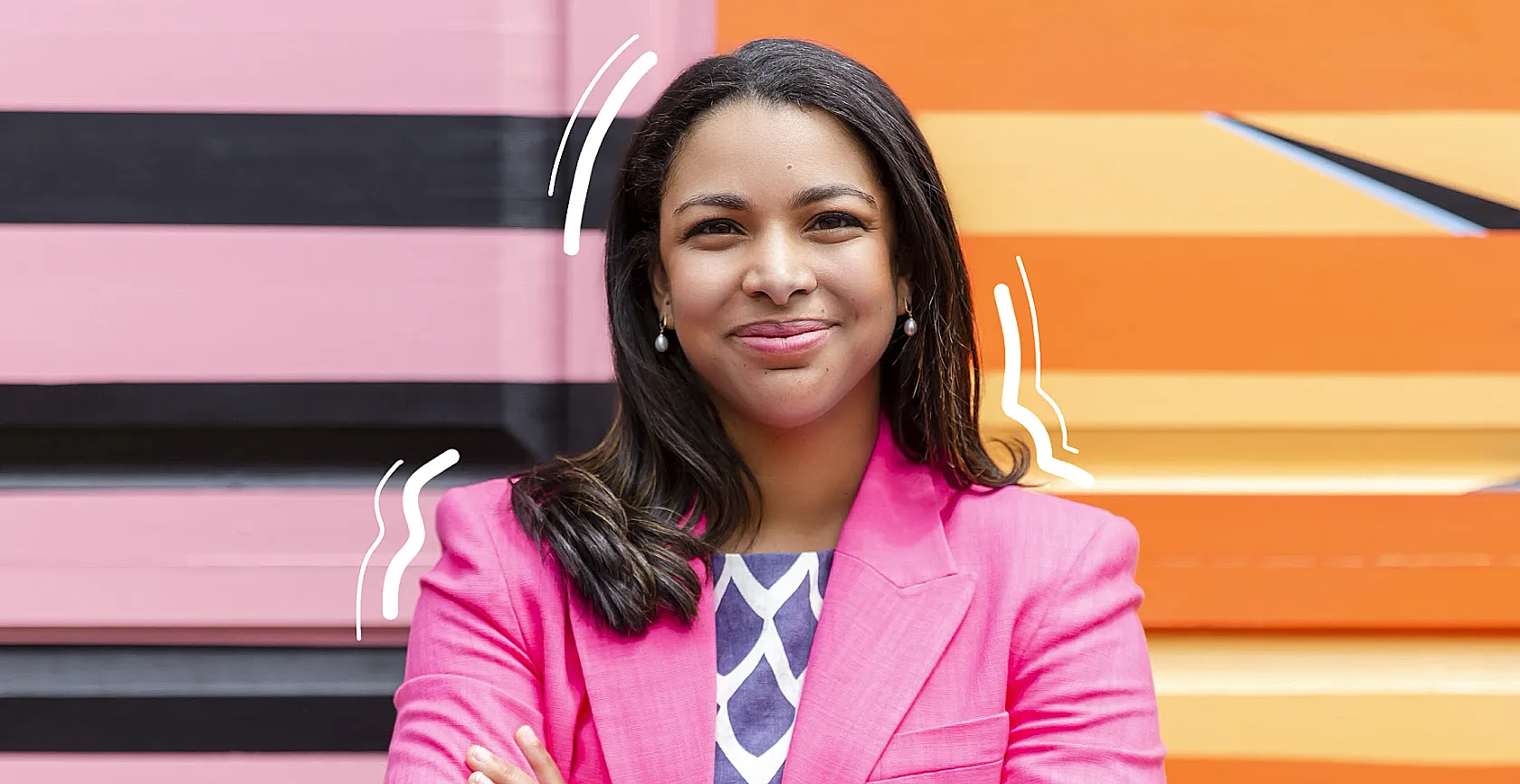